Processes
Reaction Injection Molding (RIM)
Reinforced Reaction Injection Molding (RRIM) process is a development of RIM in which common reinforcing agent such as milled fibers or mineral fillers are incorporated into the polymer to modify specific properties. Increasing the mechanical properties, reducing thermal expansion, improving sound absorption or flame retardancy are among the typical targets.
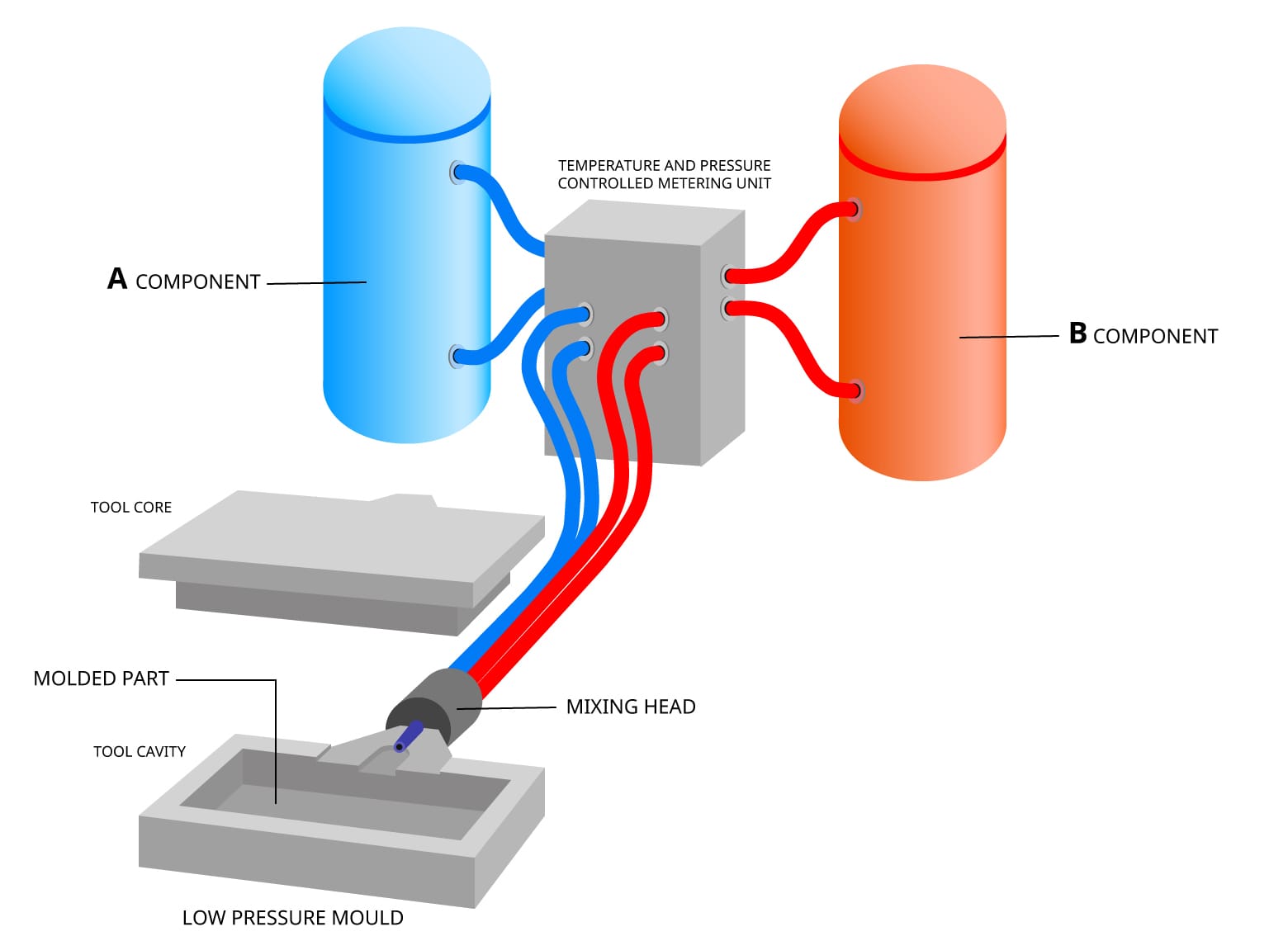
Other Processes
01
Infusion
In this process, a dry laminate fiber reinforcement is placed into a rigid or flexible mold, sealed using a special plastic film/bag, and placed under vacuum. Once all the air has been removed from the bag and the dry laminate is fully compressed, the resin is introduced, and flows through the dry laminate drawn by the vacuum pressure.
Benefits of Telene® for Infusion process
- Long injection path thanks to low viscosity
- Reduced gating points allows for fast cycle time and low consumable cost
- Higher mechanical properties due to hight fiber contents, limited porosity and absence of dry spot
02
Fast Resin Transfer Molding
(F-RTM)
Benefits of Telene® for Fast Resin Transfer Molding
- Composite parts with high fiber volume fractions and high production rates
- Good surface quality
- Fast injection and infusion allow the use of fast curing resins
- Increase permeability of fiber preform due to open mold gap
- Almost no additional resin required to push trapped air out of the mold cavityty
UPCOMING PROCESS
Pultrusion
The pultruded part is then moved to the cutting and trimming station. The shape of the cross section of the die determines the shape of the composite. The puller provides the force for the movement of materials through the entire system.
Benefits of Telene® for the Pultrusion Process
- High productivity
- Continuous process and can be completely automated
- The process can produce a composite part with high reinforcement content
- High structural properties due to very straight fiber
- Good quality surface
- Suitable for making high-volume composite parts
- High material utilization (scrap rates are usually less than 5%)
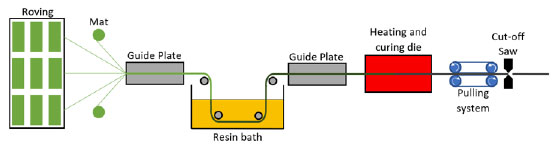